
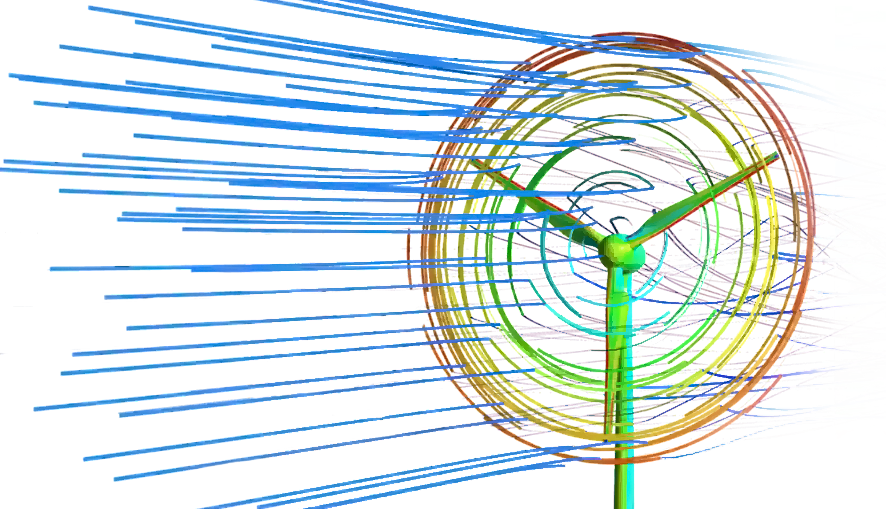
Цифровой двойник
Важной особенностью цифрового двойника является то, что для задания на него входных воздействий используется информация с датчиков (сенсоров), установленных на реальном устройстве.
Цифровой двойник может работать как в онлайн, так и в офлайн режимах. Информация, поступающая с реальных датчиков, сравнивается с показаниями виртуальных датчиков цифрового двойника, что позволяет выявлять аномалии и устанавливать причины их возникновения.
Цифровой двойник позволяет существенно расширить возможности облачных аналитических сервисов, используемых в концепции Промышленного Интернета Вещей (IIoT = Industrial Internet of Things) четвертой промышленной революции.
На этапе изготовления, разработанная системная модель (которая уже может называться Цифровым двойником изделия) поможет в определении требуемых допусков, точностей изготовления для соблюдения характеристик и безотказной работы изделия в течении всего срока службы, а также позволит быстро выявить причины неисправностей в процессе тестирования.
При переходе к этапу эксплуатации изделия модель Цифрового двойника может быть доработана и использована для реализации обратной связи с разработкой и изготовлением изделий, диагностикой и прогнозированием неисправностей, повышением эффективности работы, перекалибровки, выявления новых потребностей потребителя.
Важным аспектом успешного применения Цифровых двойников является то, что разработка устройств и систем должна вестись с учетом данной концепции, что позволит существенно повлиять на построение бизнес-процессов предприятия и создание новых сервисов услуг.
Наиболее эффективным применение Цифровых двойников является для продукции со следующими критериями:
- Сопровождение продукции квалифицированным специализированным сервисом (контроль состояния, мониторинг, техническое сопровождение).
- Длительный жизненный цикл изделия (более 5 лет).
- Большое количество экземпляров установленного оборудования.
- Широкий диапазон и многообразие условий эксплуатации.
- Труднодоступность изделия для проведения обслуживания.
Это весьма обширный список критериев, под которые подпадает продукция из различных отраслей промышленности, таких как:
- Энергетика (атомная, нефтегазовая отрасль, турбомашиностроение).
- Авиационные двигатели и авиационное оборудование.
- Сложное промышленное оборудование (насосы, приводы, пр.).
- Железнодорожные и автомобильные транспортные системы.
- Медицинское оборудование.
На сегодняшний день при эксплуатации оборудования различают три основные стратегии управления его техническим обслуживанием и ремонтом (ТОиР):
- Техническое обслуживание по событию (ТОС) или реактивное обслуживание.
- Планово-предупредительный ремонт (ППР).
- Обслуживание по фактическому состоянию (ОФС).
Техническое обслуживание по событию предполагает замену вышедших из строя деталей по факту их поломки, что зачастую увеличивает стоимость ремонта и время вынужденного простоя при проведении работ.
Планово-предупредительный ремонт является наиболее распространенным на сегодняшний день видом технического обслуживания и подразумевает замену деталей через определенные временные интервалы, которые определяются с помощью расчета среднестатистического времени наработки на отказ.
Наиболее передовым видом ТО является обслуживание по фактическому состоянию. Оно подразумевает устранение отказов оборудования путем интерактивной оценки технического состояния оборудования по совокупности данных, поступающих с его датчиков и определения оптимальных сроков проведения ремонтных работ.
Статистика говорит о том, что ключевые показатели эффективности при применении ОФС могут достигать следующих показателей:
- Расходы на техническое обслуживание – снижаются на 25%.
- Устранение аварий – на 70%.
- Незапланированный простой – на 35%.
- Производительность – увеличивается на 20%.
Цифровой двойник является одним из инструментов ОФС, который позволяет промоделировать различные варианты полных и частичных отказов, работу устройств с учетом режимов их работы, воздействия окружающей среды и различной степени износа деталей.
Компания Ansys, Inc. предлагает свою оригинальную концепцию Цифрового двойника на основе всестороннего использования технологий численного моделирования. Ведущие компании и раньше использовали численное моделирование для создания виртуальных прототипов сложных технических устройств и систем, содержащих механические, электронные и встраиваемые программные компоненты, а также для создания упрощенных моделей пониженного порядка, встроенных в алгоритмы, предназначенные для управления работой самого разнообразного промышленного оборудования. Но сегодня Интернет вещей позволяет передавать информацию от датчиков, подключенных к устройству, Цифровому двойнику в качестве граничных условий в режиме, близком к реальному времени.
Результаты моделирования с применением цифровых двойников могут быть откалиброваны на основании рабочих характеристик физического изделия или процесса. Инженерный анализ на основе технологии Цифровых двойников может использоваться для определения причин снижения производительности, оценки результатов различных стратегий управления, создания оптимальных графиков технического обслуживания и т. д. В конечном итоге технология Цифровых двойников может беспрецедентно повысить производительность и надежность изделия или процесса, снижая при этом эксплуатационные расходы.
Более подробную информацию о технологии Цифровых двойников, машинном обучении, системном и имитационном моделировании вы можете получить на сайте нашего подразделения МЦД Диджитал.